Soldering Automotive Wiring
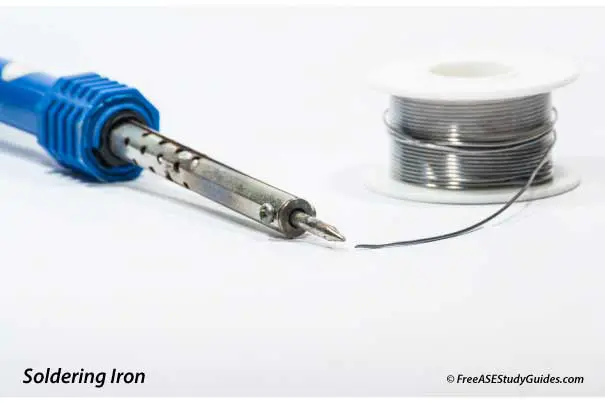
Damaged wiring can be soldered to complete or repair an automotive electrical circuit. The broken wires can be repaired without replacing the entire harness or section. Use rosin core solder; the center contains flux that cleans the surface of the wire to be soldered. Solder is often a combination of mixed alloys. Automotive applications use 60/40, containing 60% tin and 40% lead. This solder melts at about 370° F. It's vital to use a soldering iron that brings the wire up to temperature quickly.
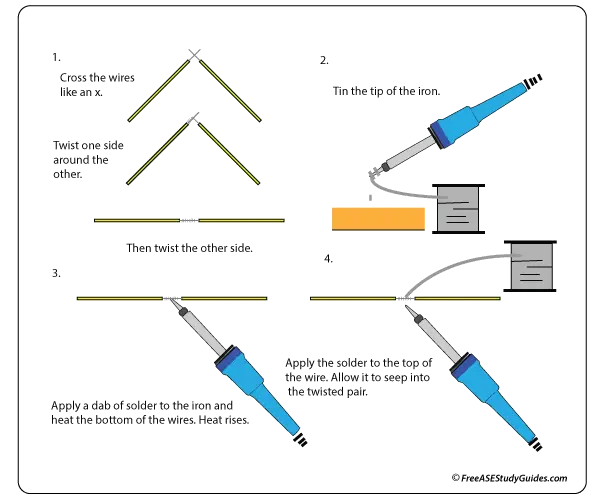
Tin the tip of the iron and then clean it with a sponge before heating the wire. Apply a little solder to the tip before applying heat to the twisted wires. Heat the wires so they are hot enough to melt the solder, then apply the solder to the twisted wires, not the tip of the iron. Applying the solder to the iron tip may be tempting because it's fast but only leads to a cold solder joint.
A cold solder joint is brittle and porous, resulting in excessive resistance in the joint and the circuit. This can also happen by moving one of the parts before the solder has hardened. The solder should flow into and around the twisted wires. Use shrink wrap with an adhesive on the inside, and be careful not to overheat. Heat the shrinkwrap with a heated drier, the iron tip, a torch, or a lighter.